Description:
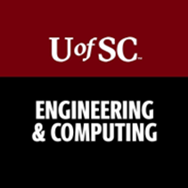
Reference #: 01611
The University of South Carolina is offering licensing opportunities for Computer Aided Process Planning Software
Background:
Automated Fiber Placement (AFP) is an additive manufacturing technique using strips of composite material that is employed in the manufacturing of large aerospace structures. The inherent complexity of the process results in unavoidable defect generation that is largely dependent on the geometry of the structure. Process planning is the matchmaking between a design and manufacturing, and proper planning can help to eliminate many predictable defects. However, this process is currently very manual, complex, and time-consuming.
Invention Description:
The Computer-Aided Process Planning (CAPP) software provides a method for assessing a multitude of inputs to process planning, optimizes said inputs, and provides the manufacturer with the best possible manufacturing plan to produce the structure.
Potential Applications:
The process planning phase of Automated Fiber Placement is a time-consuming, complex, and highly manual process resulting in a bottleneck to get a design to the manufacturing floor. There is a multitude of interconnected inputs, some of which are listed below: • Layup strategies • Starting points • Material width • Stagger shifts • Defect constraints • Defect importance The main problem is that current practice is to manually select the presented inputs, among others, and attempt to assess them without any defined metric. This requires a trial-and-error process, and ply designs are often chosen based on a “first try” solution. This could mean that, for the lifetime of a part, the manufacturing is in a suboptimal condition resulting in possible material waste, lower throughput, and higher costs.
Advantages and Benefits:
The developed software can greatly reduce the amount of time and effort spent in the phase of transferring a design to the manufacturing floor. This results in a higher pre-manufacturing rate, therefore reducing labor hours and total costs. Utilizing the optimization functionalities also leads to proper input selection resulting in a reduction in the amount of effort required during manufacturing. For instance, eliminating defects to the best extent possible will reduce the amount of rework of said defects, and therefore the amount of time allotted to it. All of this combined leads to a simplified and streamlined process that reduces the cost of a part while improving manufacturing and resulting throughput through the employment of optimal inputs.
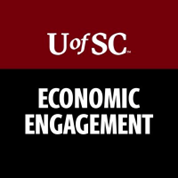
For licensing information, contact:
Nikki Biagas, Licensing & Compliance Manager- bianik@sc.edu
UofSC Technology Commercialization Office- technology@sc.edu